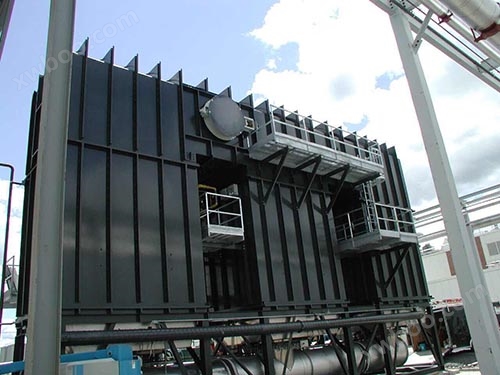
Performance characteristics of RTO products for thermal storage incinerators:
1. It can achieve fully automated control, with simple operation, stable operation, and high reliability.
2. Low operating costs and ultra-low fuel costs. When the concentration of organic waste gas is above 500PPM, the RTO device basically does not need to add auxiliary fuel.
3. The decomposition efficiency of VOCs is over 99%;
4. The exhaust gas stays in the furnace for a long time and there is no dead zone in the furnace;
5. Adopting multiple technologies simplifies the equipment, makes it easy to maintain, and reduces operating costs.
6. No secondary pollution such as NOX is generated.
The thermal oxidation method can be divided into three types: thermal combustion type, partition type, and thermal storage type. Their main difference lies in the different methods of heat recovery. All three methods can be combined with catalytic methods to reduce the reaction temperature.
1. Thermal combustion type thermal oxidizer. Thermal combustion type thermal oxidizer generally refers to gas incinerators. It consists of a combustion aid, a mixing zone, and a combustion chamber. Combustion aids (such as gas, petroleum, etc.) are used as auxiliary fuels, and the heat generated by combustion preheats the VOC exhaust gas in the mixing zone. The combustion chamber provides sufficient space and time for the preheated exhaust gas to complete the final oxidation reaction. Under the premise of sufficient oxygen supply, the degree of oxidation reaction (affecting the final VOC removal rate) depends on the "three T conditions": reaction temperature, residence time, and turbulence mixing. These "three T conditions" are interrelated, within which one condition can lower the other two conditions. One disadvantage of the thermal combustion type thermal oxidizer is that the auxiliary fuel price is too high, resulting in high operating costs for the device.
2. Regenerative thermal oxidizer. Regenerative Thermal Oxidizer (RTO) is a device that incorporates a regenerative heat exchanger into a thermal oxidation unit to preheat VOC exhaust gas before undergoing oxidation reactions. With the development of thermal storage materials, the heat recovery rate of thermal storage heat exchangers can now reach over 95%, and the occupied space is becoming smaller and smaller. In this way, the consumption of auxiliary fuel is minimal (even without auxiliary fuel, and when the concentration of VOC reaches a value above, heat can still be output from RTO). At the same time, due to the current use of ceramic fillers as thermal storage materials, it can treat corrosive or particulate VOC exhaust gases. RTO devices can be divided into valve switching and rotary types. Valve switching RTO is a common type of RTO. It consists of two or more ceramic filled beds, which change the direction of airflow through valve switching, thereby achieving the purpose of preheating VOC waste gas.
3. Partition type thermal oxidizer. Partition type thermal oxidation refers to the addition of a partition type heat exchanger in a thermal oxidation device, which transfers the heat carried by the high-temperature gas discharged from the combustion chamber to the low-temperature gas at the oxidation device, and undergoes oxidation reaction after preheating. Due to the current partition type heat exchanger achieving an 85% heat recovery rate, the consumption of auxiliary fuel has been greatly reduced. Inter wall heat exchangers are typically designed as tube, shell, or plate types. Due to the usual thermal oxidation temperature being maintained between 800 ℃ and 1000 ℃, the partition heat exchanger is made of heat-resistant stainless steel or alloy materials. This makes the cost of wall mounted heat exchangers very high, which is a disadvantage of wall mounted thermal oxidizers. At the same time, the thermal stress of the material is also difficult to eliminate, which is another disadvantage of the partition type thermal oxidizer.